April 2022 | 2635 words | 10-minute read
In 1988, India’s state-owned Doordarshan network showcased an iconic advertising campaign with the kind of recall value that brands today would pay megabucks to have. The three commercials in the campaign used inspiring lyrics and happy visuals of a developing nation, set to the accompaniment of an upbeat tune, to encapsulate the powerful contribution that one company — Tata Steel — had made towards the building of a nation. Its powerful tagline, almost an aside, flourished the perfect climax, 'We also make steel'.
Decades later, Tata Steel Ltd (Tata Steel) has moved far beyond the achievements described in those commercials. Its recent advertising tagline, ‘#WeAlsoMakeTomorrow’, now shapes every aspect of the company, across divisions, departments and functions.
Facing the future
The journey towards re-inventing the organisation began with the initiation of multiple strategic initiatives, intended to instil structural, cultural and financial future readiness. In keeping with the exhortation of the group Chairman, N Chandrasekaran, to simplify, synergise and scale, Tata Steel decided to consolidate and expand the business that generations of employees had nurtured since 1907.
But the future, as envisaged by Tata Steel’s global CEO & MD, TV Narendran, would be “tougher than the past”, so it was necessary to shed the assets and strategies that were no longer feasible going forward. The company divested itself of NatSteel, its asset in Singapore, while retaining the one in Thailand. Mr Narendran says, “We could not unlock more long-term value from NatSteel. But our asset in Thailand is structurally self-sufficient and stronger, has upstream and downstream facilities and has a low carbon footprint.”
The company decided to scale up in India. Debashish Choudhury, chief, Corporate Strategy and Planning, Tata Steel India and Southeast Asia, says, “India is the only large market with strong growth of steel consumption and that gives us a competitive advantage. We also have access to a significant proportion of our key raw material needs. Our ability to scale in India is central to our goal of being the most respected and valuable steel company in the world.”
"Our ability to scale in India is central to our goal of being the most respected and valuable steel company in the world.”—Debashish Choudhury, chief, Corporate Strategy and Planning
Tata Steel acquired key assets seen as having long-term value. From a single site at Jamshedpur, Tata Steel grew with the acquisition of Meramandali (formerly Bhushan Steel) and Neelachal Ispat Nigam, besides its own greenfield investment in Kalinganagar in Odisha.
These newer plants have the capacity to manufacture long and flat products, an advantage given India’s focus on infrastructure and the burgeoning demand for appliances, automobiles, etc. The 2500-acre Neelachal site and the 3500-acre Kalinganagar site offer huge scope for unlocking value from scale and infrastructure. Neelachal also has 100 million tonnes of iron ore. These factors, and the enhanced ecosystem, bring the company’s goal of 40 million tonnes of steel production by 2030 within reach.
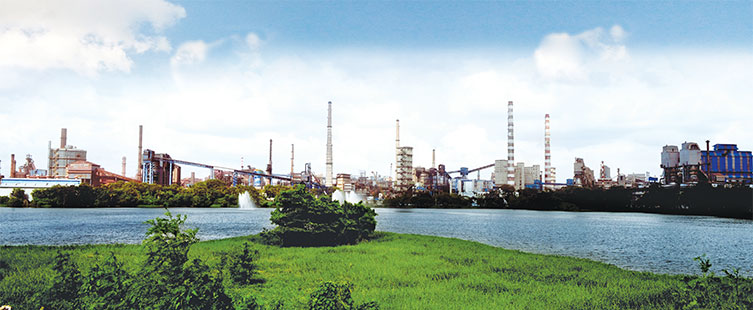
Brave new businesses
A key part of looking ahead involves moving into downstream businesses, getting into services and solution-oriented businesses and working with new materials to beat the cyclicality that the legacy business labours under.
Debashish Bhattacharjee, vice president, Technology and New Materials Business, Tata Steel, is excited about the possibilities thrown up by nascent technologies as well as the new materials that the company is banking on. “A whole new world is looming ahead on the strength of decisions made today. Being on the cusp of that future is a heady proposition,” he says.
In 2017, Tata Steel made a long list of 150 new materials with potential. Tossing out those that didn’t address future megatrends, didn’t allow for innovative applications in multiple sectors and weren’t ecofriendly, the company ended up with three composite materials, having unexplored potential, namely polymer matrix with fibre reinforcement, graphene and advanced ceramics.
“We needed to develop and scale up our technologies that would decarbonise our steel business. To do that, we had to completely recast the way we looked at technology.”—Debashish Bhattacharjee, vice president, Technology and New Materials Business
The composites had structural applications. Like steel, polymer matrix can be used to build anything from gas cylinders and railway coaches to aircraft fuselages and bridges. Unlike steel, it is corrosion resistant, mouldable and lightweight. Vehicle bodies made of this material consume less fuel.
Tata Steel has already notched up nearly Rs 200 crore of business in composite materials. The company has a JV with a Dutch company involved in the design and prototyping of railway interiors for the European market, using polymer matrix that is manufactured in West Bengal and Gujarat.
The second material, graphene, was another winner, as Tata Steel had its own patents for graphene manufacturing. Graphene has applications in corrosion resistance and in enhancing electronic products and composite materials. The company has set up a graphene plant in Jamshedpur with a capacity of 100 tonnes per annum. It has also partnered with the Ministry of Electronics and IT to set up a Rs 85-crore joint innovation centre for graphene in Kerala.
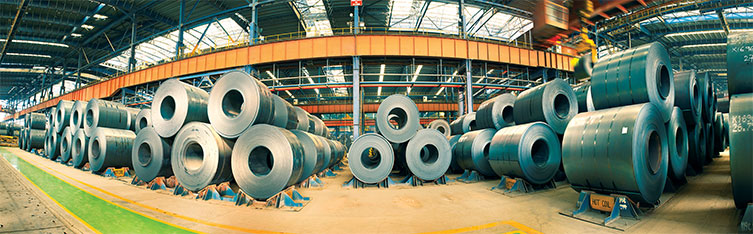
The third material, advanced ceramics, used in the steel industry for heat resistance, has applications in electronics, medical materials, space and defence. The market for medical materials is about Rs 65,000 crore and includes implants, bone replacement, collagen for the treatment of severe burn trauma, etc. The medical materials are being made in Mumbai and the collagen in Kharagpur.
Ceramics and composites already have worldwide markets in excess of $100 billion, with the Indian market at a fledgling $2.5 billion and poised to grow.
The new materials lend themselves to multiple applications, limited only by the imagination. Dr Bhattacharjee says, “Research in technology disruption is key to these businesses, which are knowledge-intensive.” Tata Steel is partnering extensively to generate knowledge and capacity in these materials.
The business, only three years old, has miles to go, but Tata Steel has ambitious plans. By 2030, it hopes to corner at least 10-12 percent of the market. “We need to study the market and supply sides of the business. That takes time and collaboration with experts,” he adds.
Renewing technology
Steel is infinitely recyclable. The downside: the steel manufacturing process ends up producing more carbon dioxide than steel. A solution to this problem does not exist yet. But given that India has signed the Paris Agreement — promising to take credible action towards reducing greenhouse gas emissions, the key reason for global warming — Tata Steel is keen to reduce its carbon footprint.
Dr Bhattacharjee says, “We needed to develop and scale up our technologies that would decarbonise our steel business. To do that, we had to completely recast the way we looked at technology.” The company mapped out seven technology leadership areas, namely carbon capture and usage or storage; production of cheap, clean and green hydrogen; use of electric power for mobility; use of low-grade ores and rejects of ores; conservation and utilisation of water; new ways of coating technology and new coating materials that are anti-bacterial and anti-viral; and advanced analytics for defect prediction.
“From being good technology adopters, our focus has changed to being a technology leader in the steel industry. For this, we have identified several technology leadership areas, including use of green hydrogen in steel value chain and carbon capture and usage."—Debashish Choudhury, chief, Corporate Strategy and Planning
Substantial work is happening in each of these areas. For instance, a pilot plant in Jamshedpur captures CO2 from the blast furnace and uses it to treat cooling water in the steel plants.

Mr Choudhury says, “From being good technology adopters, our focus has changed to being a technology leader in the steel industry. For this, we have identified several technology leadership areas, including use of green hydrogen in steel value chain and carbon capture and usage.
“Once these shifts happen, it will bring about an inflection point in the business. Till then, we will keep doing the small things right.”
Towards this goal, Tata Steel is collaborating with start-ups, research institutes and Tata companies like Tata Consulting Engineers Ltd and Tata AutoComp Systems Ltd. A vertical called Univenture scouts for collaborations, matches them with business needs, carries out proof-of-concept and integrates the start-up technology into the mainstream.
Another vertical called Ventures incubates the IP that comes from business related research into new businesses to generate revenue. The first business being incubated involves recycling steel making slag, a waste of the steel plant, into a soil conditioner. Dr Bhattacharjee says, “There is a whole pipeline of intellectual property waiting to be commercialised in this manner.”
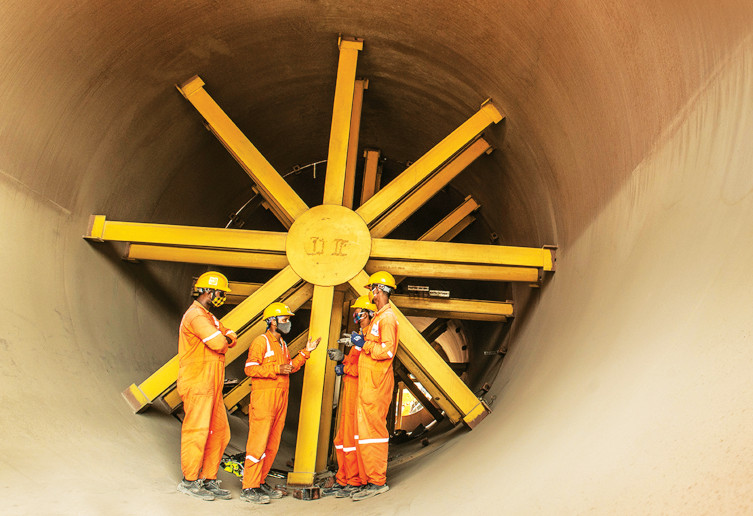
Driving sustainability
At a time when no regulatory framework existed to decarbonise the manufacturing sector, Tata Steel appointed Sanjiv Paul as VP, Safety, Health and Sustainability, and tasked him with finding ways to embed sustainability in the organisation. Mr Narendran says, “Since he was a business and operations leader, he had the credibility to drive this goal.”
The goal of sustainability wasn’t new to the company. Embedded in its vision statement is the aspiration to be the global steel industry benchmark for value creation and corporate citizenship. The framework on which the aspiration rests has four pillars: environment, health and safety of employees, community, and governance.
What needed to be put in place were the actions that would make sustainability intrinsic to the business. Mr Paul says, “Climate and biodiversity are important existential issues for life as we know it on the planet. Both need to be addressed. From being a part of the problem, we needed to become a part of the solution.”
The company invited the Cambridge Institute of Sustainability to sensitise everyone, even the union. This learning empowered the entire organisation, teaching employees to consider the needs of the business through the prism of the planet and its people.
Subsequently, Tata Steel institutionalised an internal rate of return for carbon, calculated for every capital expenditure decision in terms of its future cash flows at the rate of $40 per tonne of CO2 emission. Mr Paul says, “These actions are not demanded by regulation, but we have started taking such decisions even when it impacts our profitability.” The journey towards moving beyond compliance had begun.
“Our current assets produce steel at the rate of 2.5 tonnes of carbon emissions. We want to reduce it to 1.8 tonnes of carbon emissions by 2030 through more efficient steelmaking processes.”—Sanjiv Paul, VP, Safety, Health and Sustainability
Mr Paul says, “Our current assets produce steel at the rate of 2.5 tonnes of carbon emissions. We want to reduce it to 1.8 tonnes of carbon emissions by 2030 through more efficient steelmaking processes.” One way to do this is to increase scrap charge in the company’s steelmaking processes from the current 3-4 percent to 15 percent. Mr Paul adds, “The more scrap we charge, making it part of the circular economy, the less we need virgin iron, and hence the less emissions we have.”
Other methods to improve efficiencies include improving raw material quality and lowering emissions using fugitive heat and temperature loss. Efforts are also on to double capacity from the current 20 million tonnes to 35-40 million tonnes by 2030, using low carbon intensity processes and recycling scrap through electric arc furnaces.
Electric arc furnaces have a carbon emission of 0.4 tonnes of carbon dioxide, as against 2.5 tonnes from the blast furnace. The company has set up its first steel recycling plant, with a capacity of 5 million tonnes per annum, at Rohtak, Haryana. It is also working with the Ministry of Steel to bring in legislation to formalise the scrap collection sector in India. Mr Choudhury says, “We are innovating in the scrap collection and processing space to boost circularity in our business model.”
A lot of hope is riding on the quest of new technologies, as also on plans to work with hydrogen as the reduction agent in the process rather than carbon. Several actions are being taken to offset carbon emissions.
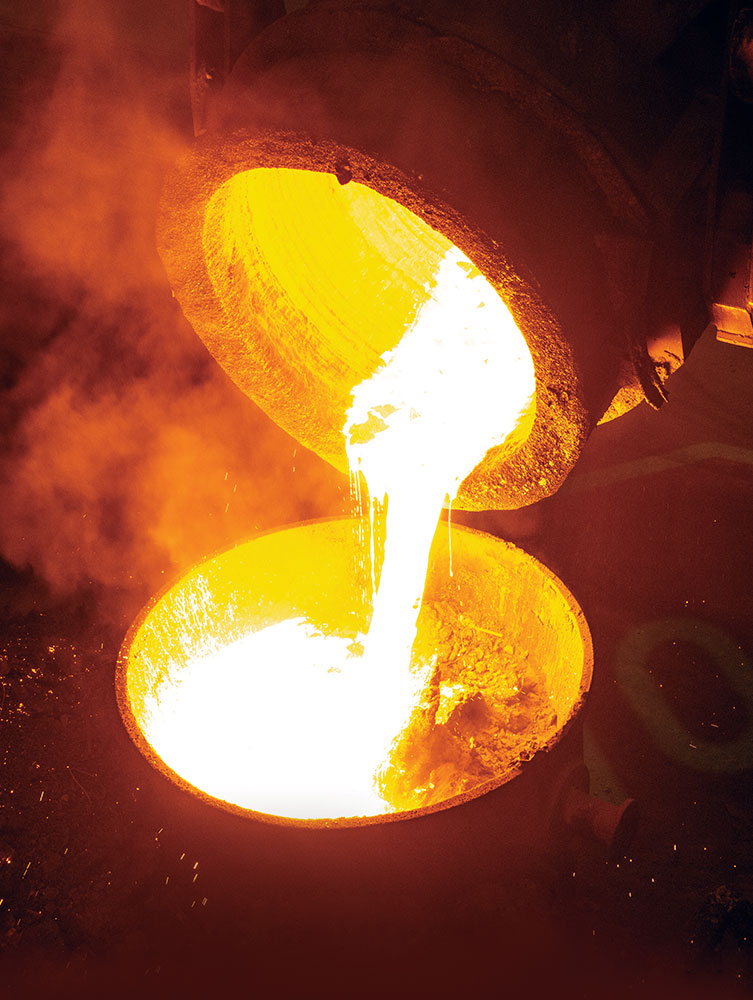
The company has started working towards reducing indirect carbon emissions from the supply chain. Mr Paul explains, “For every 3 tonnes of raw material transported to the steel plant, we are able to make 1 tonne of good steel. To reduce emissions, emerging during transportation, we deployed our bulk carrier, Frontier Sky, to conduct three trial uses of biofuel. The carrier transported over 160,000 tonnes of coal from Australia to India.” Besides intertwining sustainability with business operations to offset high carbon emissions, Tata Steel is part of two pioneering taskforces for nature- and climate-related financial disclosures. These efforts will enable cash flows to move towards more sustainable businesses.
Even vendors are required to fulfil Tata Steel’s sustainability code and exhibit ethical conduct towards their work and employees. The company, along with other steel companies and value chain partners, is part of the Responsible Steel initiative, which seeks to guide the steel industry towards complete sustainability.
Proposed targets for 2030
- Reducing carbon emissions from 2.5 tonnes to 1.8 tonnes
- Reducing freshwater requirement from 3.2 cubic litres per tonne of steel to 1.5 cubic litres
- Improving EBIDTA of by-products business by 2X.
- Sustaining material efficiency at 100 percent
- No net loss of biodiversity
Safety first
At Tata Steel, safety is a value, not just a metric. With sites housing factories, construction work and mines, safety is a hard-won victory. Mr Paul says, “Our operations come with risks, so the challenge is to ensure zero accidents. Even one death is a death too many.” The company has enhanced its safety consciousness. The SHE (Safety, Health and Environment) committee monitors the strategy for safety across departments. A reward and recognition mechanism rewards actions taken to ensure safety.
Digital architecture
Tata Steel’s digital journey began over 50 years ago, with the acquiring of its first computer in 1967. At that time, the company had the foresight to separate information technology from operational technology, knowing that both require different skill sets and security systems.
Sarajit Jha, chief, Business and Digital Transformation Solutions, Tata Steel, says, “Tata Steel has a seven-layer IT architecture in place, with data, advanced analytics and artificial intelligence enabling more informed and intuitive decisions, and enabling the transition from an intelligent enterprise to a cognitive one.” He adds, “In the recently conducted Data and Analytics Operations Model assessment Tata Steel secured 3.8 out of 5, that is a group benchmark and amongst the highest globally. We have set ourselves a target of 4.5/5 by 2025.”
The company trained over 12,000 employees on all aspects of digital. Employees were also trained on translating business problems into analytics or digital problems. The effort yielded rich dividends. The digital transformation journey has delivered around Rs 3500 crore to the company within a year of implementation.
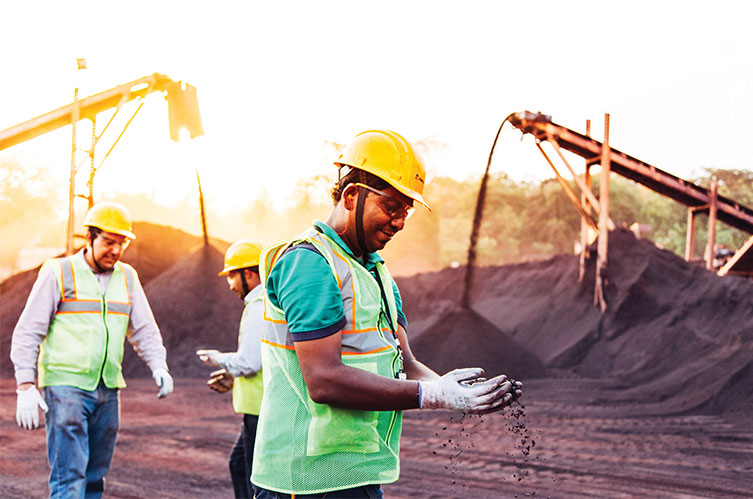
Culture of improvement
Tata Steel sees itself as the most respected and valued steel company globally. While there are metrics to assess valuation, respect is intangible. Small steps, however, can be taken that can incrementally add value to the sum total, taking the organisation in the direction it wishes to go. The company has instituted a culture in which small improvements are institutionalised. More importantly, it has ensured that this culture of doing the right thing permeates every corner of the organisation.
#WeAlsoMakeTomorrow serves as a recurrent motif that not only builds on the emotional resonance of the past but also points the way to a future in which Tata Steel continues to add value to the social and economic fabric of our lives.
—Cynthia Rodrigues