September 2022 | 3387 words | 13-minute read
The Tinplate Company of India (TCIL), now a Tata Steel Group company, was formed to meet war time requirement of packaging of Victoria brand kerosene oil for the Burmah Oil Company.
It was set-up as a joint venture with an issued capital of Rs. 75 lakhs between Burma Oil Company Limited (BOC), holding two-third of the share capital and The Tata Iron & Steel Company Limited currently, with one-third of the share capital. The Company was incorporated on January 20, 1920, with Shaw Wallace & Company as the managing agents. The registered office was at Calcutta’s (now Kolkata) Wallace House, 4, Bankshall Street with the proposed site for production at Golmuri village, three miles from Tata Steel Works in Jamshedpur.
The new company appointed the American firm, Perin & Marshall as Consulting Engineers. Structural steel for the plant and some of the machinery arrived from U.S.A. and U.K. by November 1921 and within a year, the plant was up at Golmuri.
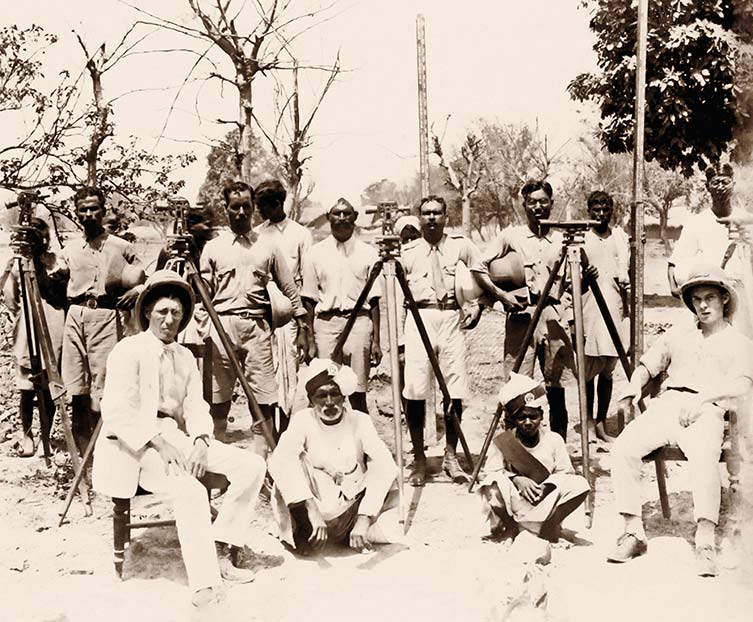
With the first Hot Dip Plant in place, finished Tinplate rolled out by December 18, 1922. By April 1928, the Victoria brand of kerosene oil produced by Burmah Oil was packed in cans made from the tin sheets produced at TCIL.
Right from the days of conception in 1907, the Tata Steel Board of Directors were aware of the opportunities that the steel industry is likely to offer in the form of bye-products like coke ovens and ancillary industries. Focusing on the job on hand they kept on hold these opportunities till the company was strongly established. After having gained confidence, post World War I, they started looking out for partners with talent and experience to co-operate with them in their expansion plans.

During this phase, Tata Steel acquired or promoted a number of units either as subsidiaries or as independent companies for producing commodities having forward or backward linkage with steel. However, one company set-up in early twenties survived the post-war slump and the depressionthat came later. That was the Tinplate Company of India.
By 1917, electrically driven blooming mills were in common use in the United States and the old steam-driven mill became a nightmare to C.P. Perin, the Consulting Engineer, entrusted with the task of running the Steel plant. It was obvious to him that Tata’s needed a new, electric bloomer, one large enough to take care of all production increases for years to come. Complete with soaking pits and buildings, such a blooming mill would cost from three to five million dollars and would accomplish only a slight boost in production. Perin didn’t see how he could swing it. He sat around with Burjorji Padshah, a trusted lieutenant and protégé of Jamsetji Tata, for days mulling over figures. Padshah was entrusted with the study of all subjects which interested Jamsetji Tata and however varied the subjects he tackled each one in a masterly fashion.
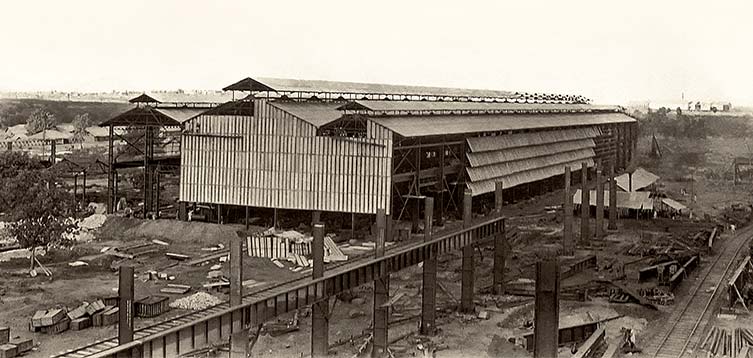
They discussed the matter of imported galvanized-iron sheets, of which India had been bringing in some 300,000 tons a year for a long time. There were also the 50,000 and more tons of tinplate used every year by the Burma Oil Company to make kerosene and petrol cans. While Padshah and Perin were trying to justify spending the money for the new bloomer, the Burma Oil Company came along with the answer. They offered to go into partnership with Tata’s in a tinplate company, furnish two-thirds of the capital, and take up the debentures, if Tata’s would make them sheet bar. Here was an outlet for another 100,000 tons of ingots a year. Tata was to start manufacturing immediately. Tin bar could be rolled on the same mills as sheet bar. India was still importing over 100,000 tons of merchant bars yearly, flats and rounds. But billets to feed a large merchant mill could be rolled on a new sheet-bar and billet mill. The market was there, suddenly, before their eyes. All they needed were the new mills which demanded staggering amounts.
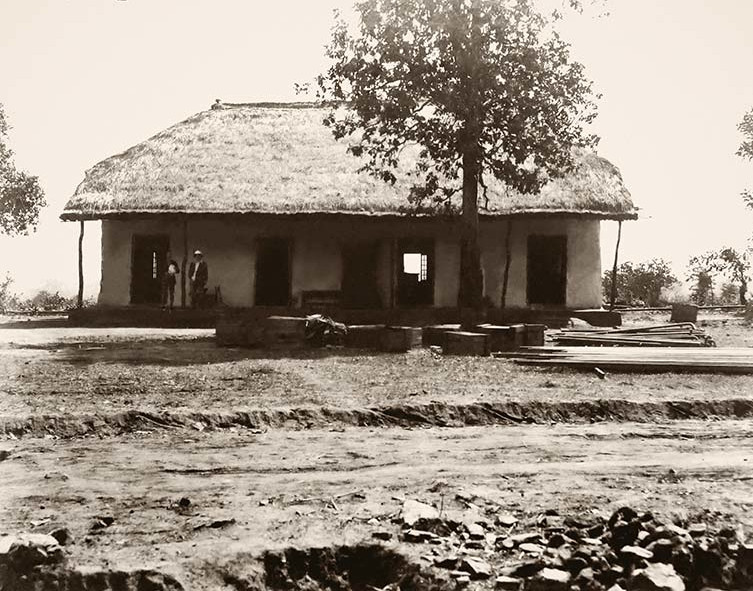
Raising production to half a million tons of ingots a year meant more blast furnaces to furnish the pig-iron requirements; then new coke ovens to supply fuel for the blast furnaces. To ensure a steady flow of fuel they would have to buy or lease more collieries. Nor was that the end. They must locate new iron-ore properties, manganese-ore veins, limestone quarries. The new steel venture took on exact shape, even though its proportions were still staggering to both Padshah and Perin. Sir Dorabji Tata and his brother, Sir Ratan Tata, and their cousin, R.D. Tata, as well as the board of directors, were backing them.
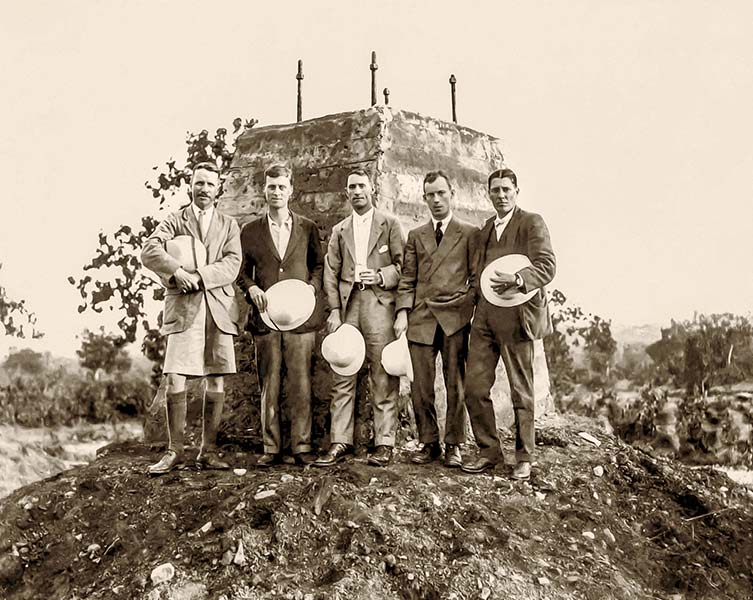
South Wales (U.K.) is the birthplace of the industry. Hundreds of years ago, the Welsh rolled iron into sheets between stone rollers until specialised equipment was gradually evolved. From Wales the industry migrated to the United States of America, followed by skilled Welsh tinplaters.
Nearly all the European workmen at the Tinplate Company, were men from South Wales. They had signed contracts to work in India for a stipulated salary, with bonuses on production at a base rate to be set after the new mills had a fair run. When the first two of the nine mills had been in operation for a short while, the management compared their production with that of the American and Welsh mills, and even allowing for local climatic conditions, they made a very poor showing.
Perin’s partner, Frank L. Estep, the general manager and the superintendent of the Tinplate decided to take the Welsh boys on. They took over one mill, worked it for an eight-hour period, and turned out a remarkably big tonnage. Then they bet the three best Welsh boys that they could beat them the following day. Naturally the Welsh rollers won the bet, but by only a few boxes of tinplate. The losers paid for plenty of drinks all round. Then the management announced the base rate, figured on the production of the Welsh rollers.
The contract workers decided to strike. After a few weeks their committee called on the Deputy Commissioner in Chaibasa and stated their case in a long and courteous hearing. The Commissioner, Jim Scott, then excused himself, leaving a supply of cold beer and a decanter of whiskey for the men, and drove to Jamshedpur to hear the company’s side of the case. He also read the contracts, signed and stamped in London and again in India. Back in Chaibasa, he told the committee the men didn’t have a leg to stand on, they had broken their contracts and forfeited their return passage to England. He advised them to go to Jamshedpur and throw themselves on the mercy of the company.
The committee was pretty well oiled by this time, and they couldn’t believe their ears. Back they went, however, meek as could be, and did what they were told. The next day the strike was over. The men accepted the base rate and turned-out production equal to the American mills and higher than their countrymen were making on similar mills in South Wales.
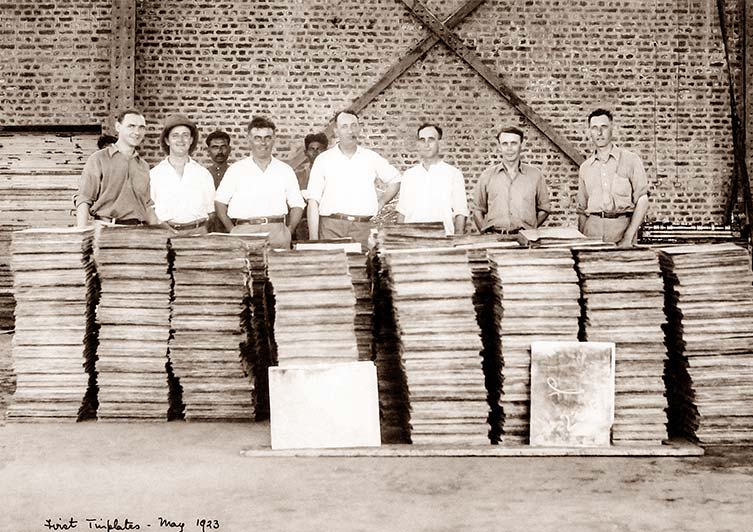
Tinplate would provide the Tata Iron and Steel Company with an outlet at its very door for a considerable portion of the increased output of steel available from that company’s greater extensions. The steel company agreed to supply the new company with 35,000 tonnes of steel bars annually.
Since inception it has been a long and hard journey for the pioneer of tinplate production in India. It is mainly used for the manufacture of cans for petroleum and its products, viz., kerosene oil, petrol, lubricating oils, greases, etc. Subsequently, these are used as containers of vegetable oils, ghee, molasses and other products, and finally provide for the handicraft of the bazaar tinsmith in the shape of toys, small oil lamps, syringes, etc. By 1923, TCIL rolled out its first finished tinplates and products that appeared in the market in the form of kerosene tins.
For making containers of perishable goods, tinplate is one of the indispensable materials. Consisting, as it does of a thin sheet of steel, it makes an exceptionally light weight and lasting packing material at a low cost. Tinplate is rolled from steel bar of a suitable analysis into various gauges and coated with tin to a brilliant surface. The steel imparting strength to the cases made out of it and the coating for which the purest tin obtainable is used, preventing rust.
Maintaining the balance: World War II
With the outbreak of World War II, the company faced the worst crisis in its history as supplies of both tin and palm oil from Malaysia were restricted. Making an all-out bid to keep operations going through the war years, TCIL diversified into the manufacturing of un-tinned black plates used in Jettison tanks for the royal air force. To augment production, it also took over processing of steel from sheet mills of Tata Steel.
During the battle of Waterloo, Napoleon found it increasingly difficult to feed his troops who were said to have marched literally on their stomachs. To tide over this crisis the French Government offered a prize of 12,000 francs to anyone who could develop a new and effective method for preserving food. An obscure, unknown chef worked out a method for preserving food in bottles and won the award.
Later on, another person who read the reports of the work, came up with the idea to substitute the fragile bottle with its understandable cork stoper into a cylindrical canister made of tinplate. Although tinplate had been around since 1240 AD, it did not come in to its own until the advent of tin can for food preservation. Since then it is a story of a triumphant march for tinplate as a packaging material which is obvious, from the fact that tinplate production has increased manifold.
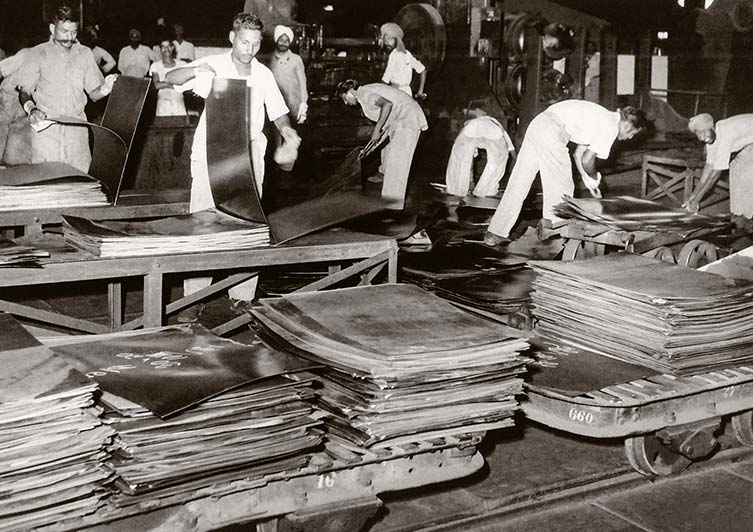
Surpassing expectations: Creating records
Tinning, rolling, and finishing technology underwent a revolutionary change. TCIL decided to modernise the Golmuri works through adoption of latest tinplating technology as was being used worldwide. Production from existing mills touched 82,778 tonnes in 1963, though the mill had a rated capacity of 28,000 tonnes, a remarkable achievement for the company!
Over the years, the Company with sense of enterprise, foresight and excellence managed to grow and capability to make its presence in various applications of everyday life, namely in edible oil, processed food, paints and pesticides, aerosols, batteries, and crown caps. Its versatile repertoire is perfect for the product and the planet, ensuring a greener future with electrolytic tinplate and tin free steel. “THINK NATURE, THINK TINPLATE” has been a recurring theme for our promotional activities.
The registered office of the company continues to be at Kolkata from the time of its inception. It became a public company in 1961 and undertook an initial public offering (IPO) of equity shares in 1975. In 1986, TSL acquired the entire shareholding of BOC in the company. With 74.96% shareholding in TCIL, Tata Steel continues to view the company as a key portfolio. TCIL thus works in alignment with the Tata Steel ecosystem and participates in all Tata group platforms and activities.
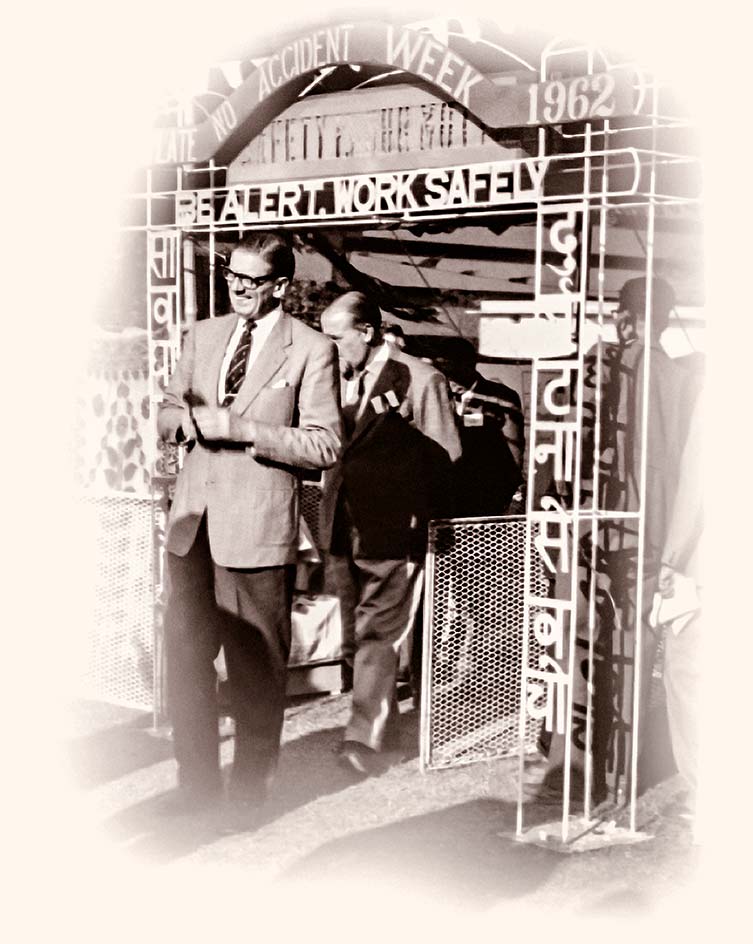
Employee welfare: Caring for the community
From its inception, employee health and welfare were envisioned as the core values of TCIL, striving to build a better tomorrow for all stakeholders.
Provision for erection of 100 additional Indian quarters was sanctioned for employees in 1935. TCIL had its own works hospital and overall healthcare set up right next to its plant. In 1941, a small crèche was added to the works hospital. The company had also initiated work safety practices as early as in the 1960s.
TCIL has been equally devoted to multiple community development programmes for healthcare, education and employability and sought to build a greener future in true Tata traditions.
Admirable efforts in the sphere of Education are directed towards ensuring educational equity for the underprivileged. Sustainable and inclusive learning forms an intrinsic part of the initiatives under Education through - Pre-Nursery Classes for toddlers: With the objective to provide coaching to small children from the underprivileged sections of the society, helping them secure admission in formal schools (primarily English medium).
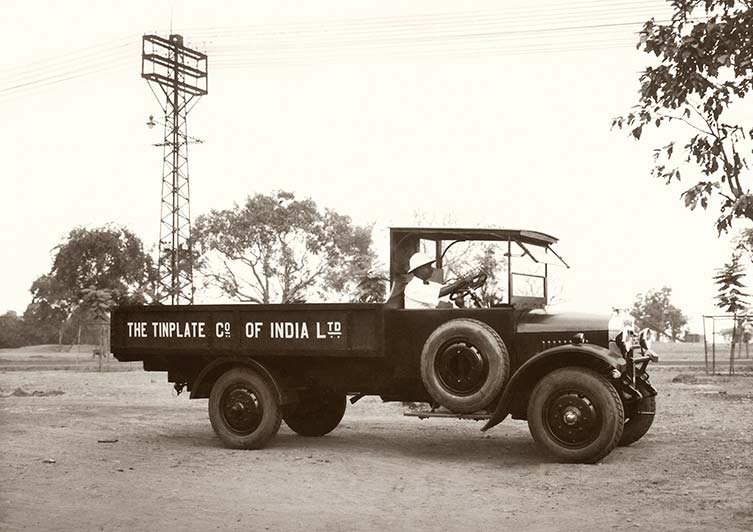
TCIL runs a total of six Remedial Coaching Centers in economically backward areas of Hurlung Panchayat, located within 5-6 kms from the Works. The program identifies school dropouts and academically weak children and provides special coaching to enhance their academic performance, reducing their failure and dropout rate.
In partnership with Tata Steel Rural Development Society (TSRDS), TCIL has set up Masti Ki Pathshala - a first of its kind All-Boys Residential Bridge School for street children to transform their lives through holistic education and bring them to mainstream and make ready for private English medium schools.
Tinplate supports 10 Government affiliated community schools within the Tinplate command area, through facilitating participation in the Tata Education Excellence Programme (TEEP). This initiative helps the schools in self-assessment and sustain continuous improvement. The schools participating in TEEP have shown visible improvement in academics and extra-curricular activities. Recently, mini science centers have been set up in some of the schools.
With an objective to enhance employment opportunities for tribal girls undertaking Community Health Provider (CHP) Training at the Tinplate Hospital, TCIL encourages them to pursue the General Nursing and Midwifery (GNM) training at the Mercy School of Nursing, Jamshedpur. Candidates who qualify the entrance test for GNM, are supported by sponsoring course fees and other expenses. TCIL also works in association with the Society for Children’s Welfare for Girls from the BPL category. Every year, 10 deserving girls receive scholarships to pursue the GNM course at Government accredited institutions in West Bengal.TCIL, at its Community Development Centres organises classes in Tailoring and Stitching for girls; specialised training in skills crochet, cross-stitch, embroidery etc.; beautician course; basic computer courses; spoken English; community health provider – CHP (semi nursing) courses and many others.

Healthcare for the community has been an integral part of TCIL’s CSR activities. Blood Donation Camps, aiding cancer patients at Tata Medical Center – Kolkata are a few examples of it.
TCIL extended its support during COVID towards the areas of most affected through various means.
Overcoming the odds: Moving ahead
TCIL was ready to adopt new technologies, a breakthrough as the company entered into an agreement with Wean United U.S.A. the world’s most experienced suppliers of tin-mill equipment, to switch to Electrolytic Tinning Process. In 1979, ETL1 was commissioned on its land kept aside for expansion with a capacity of 90,000 tonnes per annum. It was capable of producing tinplate and tin free steel. A wider range of products, including thinner tinplate were added for the first time to TCIL’s product basket. TCIL quickly metamorphosed into a leading corporate brand with a product par excellence in time. Strategically it became leaner, and quality focussed, conforming to international standards.
As a backward integration step, TCIL set-up its first Cold Rolling wStaff quarters.wThe first TCIL ambulance. Mill Complex (CRM-1) in 1996 for captive production of TMBP (Tin Mill Black Plate) for feeding the tinning line and phased out the operation of Hot Dip Plant (HDP). This did away with the dependence on imports and uncertainty associated with imported TMBP coils in terms of price and availability. Later, TCIL entered a conversion arrangement with Tata Steel in 1998.
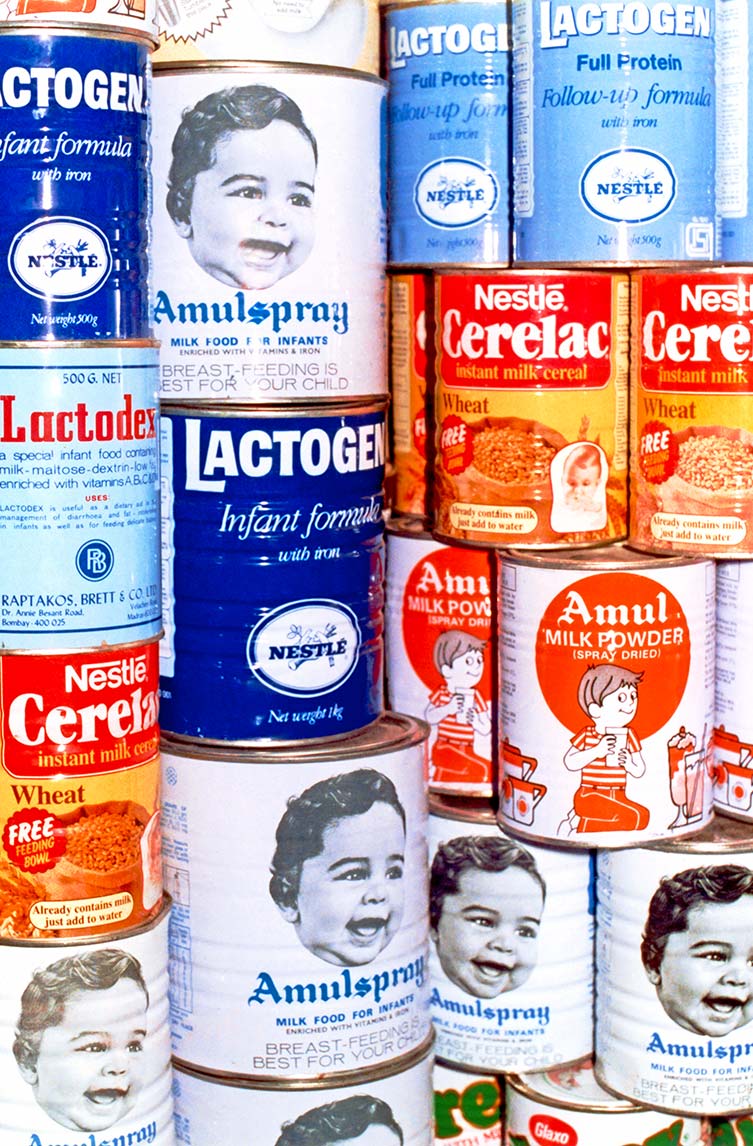

Optimising operational efficiency: Entering the 21st century
The new millennium came with its own challenges that entailed streamlining operations and processes and driving productivity to overcome market conditions. The company adopted a program “Total Operational Performance (TOP)” to drive operational excellence. This enabled the company through various debottlenecking, infrastructure strengthening, and balancing projects and helped to increase the tinning line capacity to 1,80,000 MT - generating the momentum for a 100-year race.
Creating value: Stepping towards downstream products
With production and processes in fine fettle, it was time for forward integration and injecting greater value into existing products. TCIL invested in a state-of-the-art Printing and Coating line in 2005. This created a win-win situation for TCIL and its customers by way of offering a sophisticated high-quality product and reducing supply chain inefficiencies. The supply from these lines ensured improved differentiation, and enhanced packaging life.

Thinking bigger: Attaining market leadership
As markets expanded, so did TCIL’s output. It doubled capacity in 2008 with commissioning of the second Tinning Line (ETL-2), enhancing the company’s nameplate capacity to 379,000 MT per annum. The investments backed by improved process performance helped the company to sustain its leadership position in India. TCIL also started exporting as a strategic measure – and continues to do so (~20 to 25% of its production) to discerning markets across the world, from South-East Asia to Europe, including the Middle East.
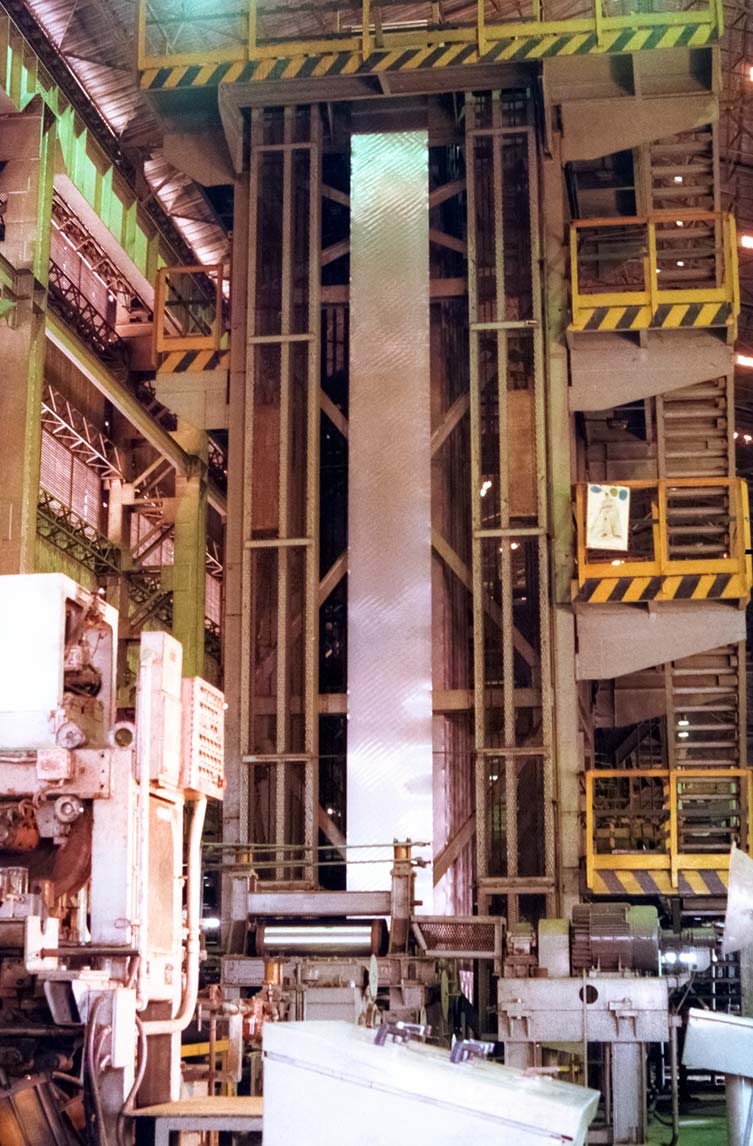
Constant thrust for operational excellence and leveraging internal capabilities the company set up its second Cold Rolling Mill (CRM-2) facility around 2012 to meet the requirements of TMBP coils to feed the second tinning line ETL-2.
All round efforts to ensure optimized manufacturing processes brought in laurels to the company by being presented the TPM consistency award in 2019 by JIPM.
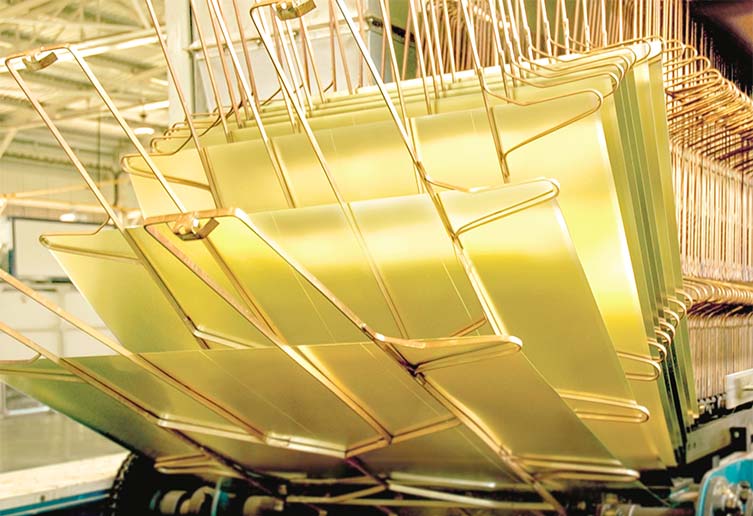
Branding: Getting closer to fillers
2018 marked the birth of ‘PAXEL’, India’s first branded tin can for packaging edible oil. Produced in TCIL’s Service and Solution Centres, PAXEL sales scaled up in no time due to its adherence to timely availability, process hygiene, safety, and overall product quality. TCIL selected some of the finest can-makers of the country as Service and Solution Partners (SSPs) and partnered them to move closer to edible oil brand owners. The assurance was a high-performance product made from genuine, best quality tinplate manufactured by TCIL. By deploying a robust supply-chain management, PAXEL services were aligned to the growing demand for better quality cans for port-based oil hubs, thus ensuring immediate success.
After completing its 100th year in 2020, TCIL, with an annual capacity of 3,79,000 MT, enjoys a pan-India presence and is sought after at 24 export destinations as well. Sustainability embedded into its DNA, it celebrates aesthetics in its applications, professionalism in its protection, toughness with technology and softness with nature.
TCIL has been working closely with Tata Steel Europe to develop products for its customers and drive operational excellence. The Tinplate Solution Centre at the Jamshedpur plant recently introduced printing and lacquering facilities to further customise and enhance the product. The centre makes ready-to-use tinplate, with the options to print or emboss the surface, all that can makers have to do is just fold and seal the cans.
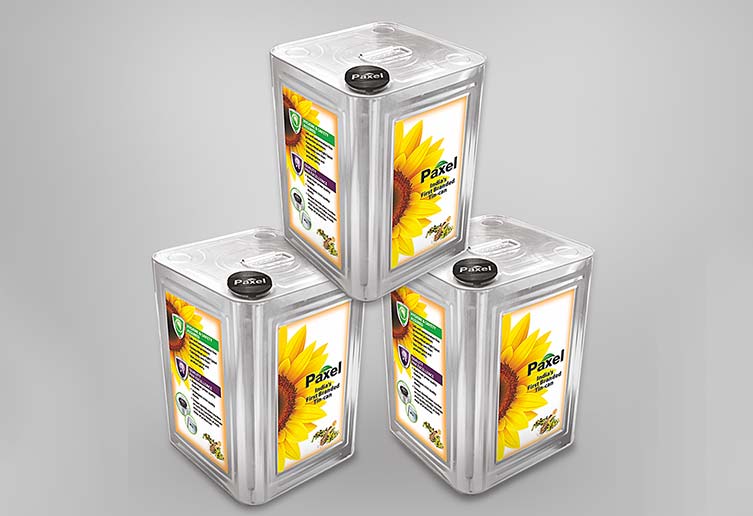
Shaping the future: Focusing on sustainable growth
For 100 years, TCIL has served the nation with pioneering products and services. The market growth and investments in the past two decades have dramatically impacted its performance. The company achieved 100% capacity utilisation in 2021-22.
The demand for tinplate is poised to grow faster than it did in the last 100 years and beyond, driven by packaging integrity, food safety, and environmental protection. Devoted to nature, touching lives across the board, TCIL leads the tinplate revolution, remaining NaturAlly No1.
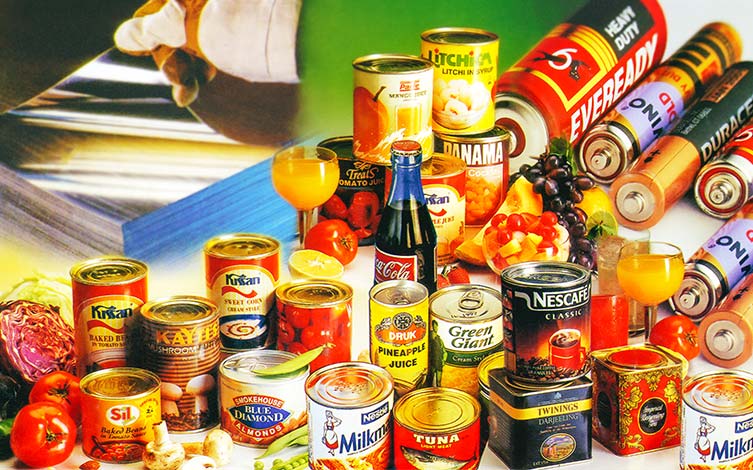
However, the penetration of tinplate in India continues to be low when compared with other countries. The quantity of tinplate required for processed foods such as fruits, fish, gherkins or even tomato puree is huge; but India hasn’t been too big on processed foods yet. The changing Indian palate and rapid urbanisation are trends that TCIL is looking to tap into. “While tinplate offers several advantages in terms of shelf life, retaining aroma, and tamperproof packaging, cost is still a big consideration in product packaging, as cheaper materials are available in the market. Tinplate will have to innovate to be a real solution provider," says R.N. Murthy, the Managing Director.
The company is now poised for its next level of organic growth as it embarks on setting up of its new tinning line and cold rolling complex – to take its name plate capacity to 679,000 TPA tinplate producer.
The author, RP Narla, is archivist, Tata Central Archives.
Photographs courtesy Tata Central Archives