June 2022 | 1570 words | 6-minute read
In the early 2010s, Tata Steel was executing a brownfield project and expanding its steel production capacity by 3 mtpa. This was a massive project and required tens of thousands of workers to arrive at the earmarked sites. Sometimes up to 80,000 personnel a day. Even without the construction labour the Jamshedpur plant has a footfall of close to 20,000 contract labour on a daily basis for regular operation & Maintenance. Most of these personnel arrived in bicycles. Traffic safety was difficult to manage. Many experiments were tried, tested, and discarded.
Then at a senior level oversight meeting, the leadership team had an idea: why not make all workers park their cycles at the site entrance and be transported by buses to the sites? The plan wasn’t simple. It required considerable planning and coordination, but it was achieved, and the safety record stayed unblemished.
Says Sanjiv Paul, vice president, Safety Health & Sustainability at Tata Steel: “It seems a no-brainer now. But the fact is it took some time for this idea to occur to us. We learned from it and have started to think differently about how we view safety.”
Backed by values
The group has been known to espouse employee-centric policies ever since its founding. At the Empress Mills in Nagpur, one of the first businesses of the group, our Founder Jamsetji Tata implemented employee welfare initiatives that were unheard of at that time. He instituted a Pension Fund and began to pay accident compensation. To ensure employee safety and well-being, he installed humidifiers and fire sprinklers in the mills — a first for India.
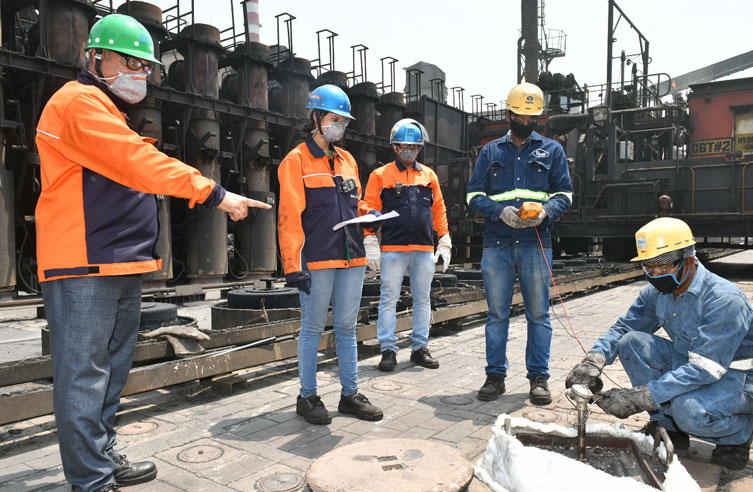
In 1979, Tata Steel instituted a hitherto new practice; it deemed a worker to be ‘at work’ from the moment he left home for the factory, and until he returned home from work. The policy continues: the company is financially liable if any mishap takes place on the way to and from work. This was a pioneering step in the industrial sector in India.
At the Empress Mills in Nagpur, one of the first businesses of the group, our Founder Jamsetji Tata implemented employee welfare initiatives that were unheard of at that time.
“When we become a multinational company some 15-odd years ago, we started thinking and acting on safety with much more passionate resolve,” says Mr Paul. “We are now directing all our efforts to be risk intelligent and to ensure Zero Harm. That is the target.”
Safety is a moving target
“After oil and gas, process manufacturing industries are the most accident-prone. Yet, most incidents happen on the road,” says Neeraj Sinha, Chief Safety at Tata Steel. “We have used artificial intelligence (AI) to institute intelligent traffic mechanisms in our campuses to ensure maximum safety.”
Vehicular speeds are monitored using devices, patterns are learnt, and AI is used to optimise movement. For example, no vehicle can move over 30kmph inside the campus, and if it does, consequence management kicks in. Automated number plate reading ensures tracking and compliance.
Similarly, Tata Motors, given the nature of its industry, is deeply involved in maximising safety in human-vehicle interaction points at its plants. A data-driven approach enabled Tata Motors to identify Critical to Safety stations, where the probability of incidents was high. Focused and time-bound efforts in the form of hazard elimination, substitution and engineering controls were taken to improve safety at these stations, resulting in 65% reduction in incidents in the past year.
As data showed that vehicular movement was the major contributor for campus incidents, Tata Motors conducted Kaizen activities to reduce risk at all human-vehicle interaction points at its plants with a focus on improving Safe Driving and Safe Walking standards.


The Titan Company too, considers travel safety as a critical element of their overall safety approach. Safety requirements are a part of the company’s travel policy, and all employees are trained in defensive driving and road safety. This extends to cabs engaged by the company and travel providers, and to material handling equipment.
While studying a pattern of incidents in material handling, Titan realised these were recurring because unqualified workers were operating the vehicles. Thereafter, Titan ensured that all material handling equipment operators should possess an LMV (light motor vehicle) license and undergo periodic training, evaluation and certification. A biometric mechanism in the vehicle’s ignition system ensures that only certified drivers operate these vehicles. This has resulted in zero safety incidents in material handling.
In the design
Titan’s safety vision is to “be the safest organisation in the eyes of all our stakeholders”. The commitment ensures that the safety charter is adopted right from the top and extends to vendors and contractors.
Titan believes that safety and health start at the design stage itself. The company helps to eliminate or control incidents at the design stage of machines through judicious design decisions and engineering. This also extends to retail store design. Safety professionals are part of design development and vice-versa, and design engineers are trained on hazard management. Thus, safety principles undergird the aesthetic design of the Titan brand.
Safety professionals are part of design development and vice-versa, and design engineers are trained on hazard management
In its manufacturing processes, the luxury products manufacturer follows the principle of ‘inherently safer design’ in which hazard elimination or minimization is in-built. Take for example, the power press, machinery that is used to cut, shape or form a metal design. Titan discovered that employees were not using the hand-pulling safety device while operating the machine, resulting in accidents. It introduced sensors in the device, whereby employees could not operate the press without the safety device. This change helped Titan achieve zero accidents in the press shops.

Titan believes that safety and health start at the design stage itself. The company helps to eliminate or control incidents at the design stage of machines through judicious design decisions and engineering. This also extends to retail store design. Safety professionals are part of design development and vice-versa, and design engineers are trained in hazard management. Thus, safety principles undergird the aesthetic design of the Titan brand.
Safety professionals are part of design development and vice-versa, and design engineers are trained in hazard management.
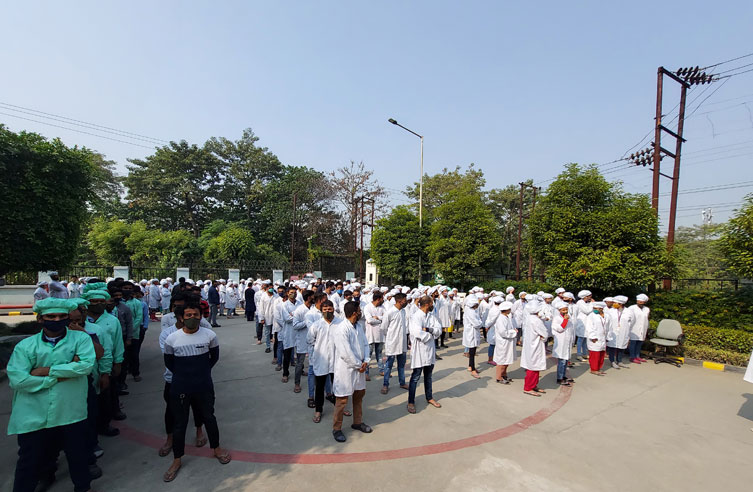
In its manufacturing processes, the luxury products manufacturer follows the principle of ‘inherently safer design’ in which hazard elimination or minimization is in-built. Take, for example, the power press, machinery that is used to cut, shape, or form a metal design. Titan discovered that employees were not using the hand-pulling safety device while operating the machine, resulting in accidents. It introduced sensors in the device, whereby employees could not operate the press without the safety device. This change helped Titan achieve zero accidents in the press shops.
The safety leadership development centre
Steel manufacturing, like many process industries, involves the use of hazardous gases, materials, and processes. Safety is a moving target and is never 100% foolproof, and the key is constant learning and evolution which the safety leadership at Tata Steel recognises.
The same devices help elderly workers understand their own health-related limitations and issues as well. Tata Steel, rated among the best employers in the world for many years, has employees who have spent their lifetime in the company, and ensuring their well-being, according to Mr Paul, is an important part of the job.
“Tata Steel is several organisations rolled into one. We’re an integrated steel maker — we’re a mining, manufacturing, an engineering/construction, and a logistics company at the same time. How do we ensure that we don’t let our guard down? Mapping risks is key to achieving this level of attention,
Moving the needle further, Tata Steel is ensuring that each organisation, division, and team maps safety risks with rigour. “Tata Steel is several organisations rolled into one. We’re an integrated steel maker — we’re a mining, manufacturing, an engineering/construction, and a logistics company at the same time. How do we ensure that we don’t let our guard down? Mapping risks is key to achieving this level of attention,” says Mr Paul.
These safety risks are mapped in a colour-coded ‘risk matrix’. High probability and high frequency risks are coded in red and roll up right to the top of the organisation, while others are addressed at the appropriate levels. “This is how we’re ensuring that safety risks are embedded at all levels,” says Mr Paul, “and that will eventually lead to Zero Harm.”
Jamsetji Tata wouldn’t have settled for anything less.
- Haroon Bijli